Qu’est-ce que l’atelier 4.0 ?
L’atelier 4.0 est un concept révolutionnaire dans le domaine de l’industrie et de la technologie. Il représente une évolution majeure des processus traditionnels en intégrant les dernières avancées numériques et en exploitant les avantages de l’automatisation et de l’innovation. L’objectif principal de l’atelier 4.0 est d’améliorer l’efficacité, la productivité et la communication dans les ateliers de production en utilisant des technologies numériques avancées.
Dans un atelier 4.0, les machines et les équipements sont interconnectés, permettant ainsi une communication en temps réel et le passage d’informations digitales entre eux. Ces machines intelligentes sont capables de collecter, d’analyser et de visualiser des données en continu, ce qui permet aux opérateurs de prendre des décisions éclairées et de gérer efficacement les processus de production. Grâce à l’utilisation de logiciels de management visuel et de plateformes collaboratives, l’atelier 4.0 offre une visualisation claire et précise des activités et des flux de travail, favorisant ainsi la prise de décision proactive et la résolution rapide des problèmes. L’atelier 4.0 favorise également l’automatisation des tâches répétitives et dangereuses, permettant aux travailleurs de se concentrer sur des activités à plus forte valeur ajoutée. Les robots collaboratifs, par exemple, peuvent travailler aux côtés des opérateurs humains, augmentant ainsi la productivité et la sécurité dans les ateliers.
De plus, l’atelier 4.0 facilite la personnalisation des processus de production, permettant aux entreprises de répondre aux demandes spécifiques des clients de manière plus efficace et rentable. En résumé, l’atelier 4.0 est un concept novateur qui intègre les technologies numériques avancées pour améliorer l’efficacité, la productivité et la communication dans les ateliers de production. Grâce à l’automatisation, à l’innovation et à la visualisation des activités, l’atelier 4.0 offre de nouvelles opportunités pour les entreprises d’optimiser leurs processus et d’atteindre un avantage concurrentiel dans l’industrie.
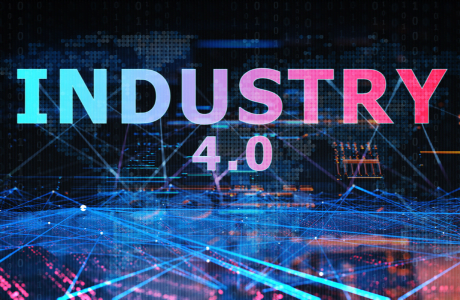
Origine et concept de l’atelier 4.0 connecté
L’origine de l’atelier 4.0 remonte à la quatrième révolution industrielle, également connue sous le nom d’industrie 4.0. Ce concept a été introduit pour la première fois en Allemagne en 2011, dans le cadre d’une initiative visant à moderniser l’industrie manufacturière du pays. Depuis lors, l’idée de l’atelier 4.0 s’est répandue dans le monde entier et a été adoptée par de nombreuses entreprises à la pointe de l’innovation technologique.
Le concept de l’atelier 4.0 repose sur l’idée de connecter tous les éléments d’une chaîne de production, des machines aux systèmes de gestion des données, en passant par les opérateurs humains. Grâce à cette interconnexion, les différents acteurs de la production peuvent collaborer de manière plus efficace et prendre des décisions éclairées basées sur des données en temps réel. L’atelier 4.0 vise à créer un environnement de production intelligent et flexible, capable de s’adapter rapidement aux changements du marché et aux besoins des clients. Le passage d’informations digitales dans l’atelier 4.0 permet une meilleure gestion des flux de travail et une prise de décision plus rapide. Les logiciels de management visuel et les plateformes collaboratives offrent une visualisation claire des activités, facilitant ainsi la coordination et la communication entre les différents acteurs de l’atelier. Grâce à l’intégration de l’automatisation, de l’innovation et de la numérisation, l’atelier 4.0 permet aux entreprises de gagner en efficacité et en compétitivité sur le marché mondial.
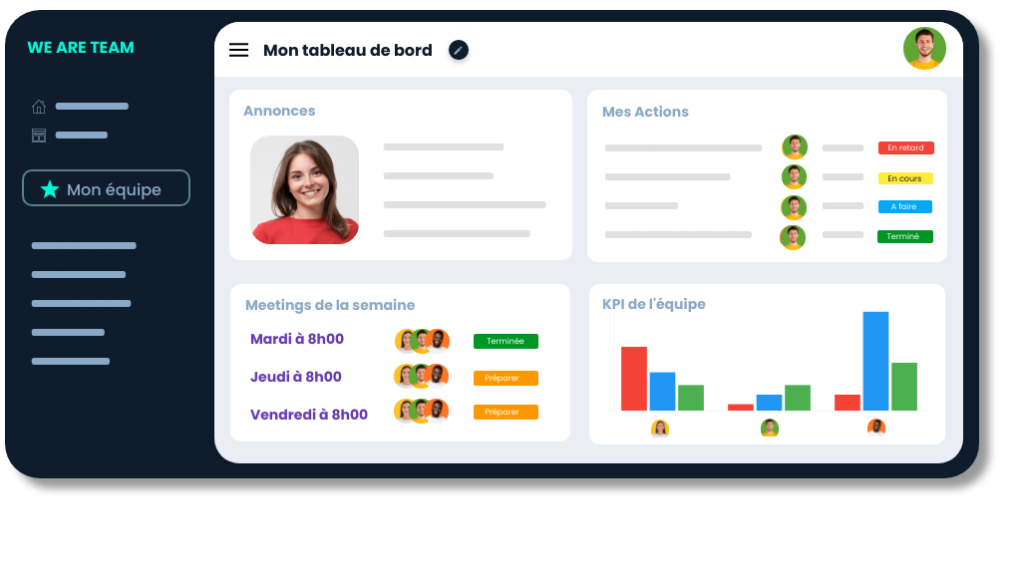
Acteurs et leaders de l’industrie 4.0
L’adoption de l’atelier 4.0 est en constante augmentation, et de nombreuses entreprises se positionnent comme des leaders dans ce domaine. Parmi les acteurs les plus influents de l’atelier 4.0, on trouve des entreprises renommées telles que Siemens, Bosch, General Electric, IBM et Schneider Electric. Ces entreprises ont développé des solutions technologiques innovantes pour soutenir la transformation numérique des entreprises manufacturières.
En plus des grandes entreprises, de nombreuses start-ups et PME se sont également lancées dans le domaine de l’atelier 4.0, proposant des solutions spécialisées et adaptées aux besoins spécifiques de différents secteurs industriels. Ces acteurs plus petits jouent un rôle essentiel dans la diffusion et l’adoption de l’atelier 4.0, en apportant une expertise et une agilité qui permettent aux entreprises de toutes tailles de bénéficier des avantages de cette révolution industrielle.
Les gouvernements et les institutions académiques jouent également un rôle important dans la promotion de l’atelier 4.0. Ils soutiennent la recherche et le développement de nouvelles technologies, ainsi que la formation des travailleurs pour les préparer aux défis et aux opportunités de l’industrie 4.0. Les partenariats public-privé sont de plus en plus courants pour favoriser l’innovation et la collaboration entre les différents acteurs de l’atelier 4.0.
En conclusion, l’atelier 4.0 est un domaine en pleine expansion, avec de nombreux acteurs et leaders qui contribuent à son développement. Les grandes entreprises technologiques, les start-ups et les PME jouent un rôle clé dans la diffusion de cette révolution industrielle, tandis que les gouvernements et les institutions académiques soutiennent la recherche et la formation pour préparer les entreprises et les travailleurs aux défis et aux opportunités de l’atelier 4.0.
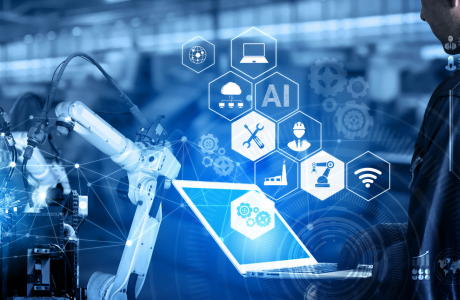
Les principes de la production connectée
Technologies des usines du futur
L’avènement de l’industrie 4.0 a donné naissance à de nouvelles technologies révolutionnaires qui transforment les usines traditionnelles en usines du futur. Ces technologies, telles que l’internet des objets (IoT), la robotique avancée, la réalité augmentée et l’intelligence artificielle, permettent une connectivité sans précédent entre les machines, les systèmes et les personnes.
Grâce à ces avancées technologiques, les usines du futur sont capables de collecter et d’analyser en temps réel une quantité massive de données provenant de l’ensemble de la chaîne de production. Cela permet aux entreprises d’optimiser leurs processus de fabrication, d’améliorer leur productivité et de réduire leurs coûts. L’internet des objets (IoT) joue un rôle clé dans la production connectée en permettant la communication entre les différents équipements et systèmes présents dans l’usine. Grâce à des capteurs intelligents et à des réseaux de communication sans fil, les machines peuvent échanger des informations en temps réel, ce qui facilite la surveillance, la maintenance prédictive et l’optimisation des performances.
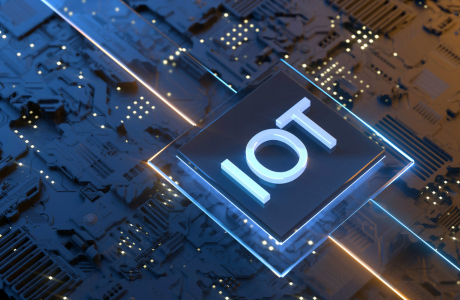
La robotique avancée permet l’automatisation de tâches répétitives et dangereuses, libérant ainsi les travailleurs pour des tâches à plus forte valeur ajoutée. La réalité augmentée offre des possibilités de formation et d’assistance virtuelle, permettant aux opérateurs d’acquérir rapidement de nouvelles compétences et de résoudre des problèmes complexes. L’intelligence artificielle permet d’analyser les données collectées et de prendre des décisions autonomes pour optimiser les processus de production.
Standardisation et normalisation
La standardisation et la normalisation jouent un rôle essentiel dans la mise en place de la production connectée. En établissant des normes et des standards communs, les entreprises peuvent garantir une interopérabilité optimale entre les différents équipements et systèmes utilisés dans leur usine. Cela facilite l’intégration des nouvelles technologies et permet une communication fluide entre les machines, les logiciels et les opérateurs. La normalisation permet également de garantir la qualité et la sécurité des produits fabriqués. En adoptant des normes de qualité reconnues au niveau international, les entreprises peuvent s’assurer que leurs produits respectent les exigences des clients et des réglementations en vigueur.
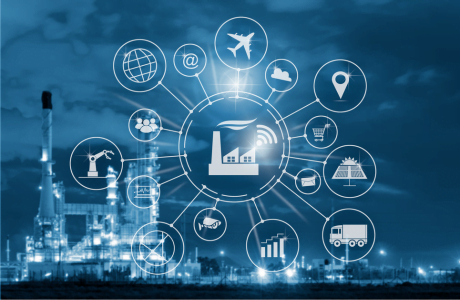
De plus, la normalisation favorise l’innovation en offrant un cadre de référence commun pour la conception et le développement de nouvelles technologies. La collaboration entre les acteurs de l’industrie est essentielle pour promouvoir la standardisation et la normalisation. Les entreprises, les organismes de normalisation et les gouvernements doivent travailler ensemble pour développer des normes harmonisées qui favorisent l’adoption de la production connectée à grande échelle. En encourageant la coopération et l’échange d’expertise, il est possible de créer un écosystème favorable à l’innovation et à la croissance de l’industrie.
En conclusion, les technologies des usines du futur et la standardisation sont des éléments clés de la production connectée. En exploitant les avantages de l’internet des objets, de la robotique avancée, de la réalité augmentée et de l’intelligence artificielle, les entreprises peuvent améliorer leur efficacité opérationnelle et leur compétitivité. La standardisation et la normalisation permettent quant à elles d’assurer une interopérabilité optimale et de garantir la qualité et la sécurité des produits fabriqués. En combinant ces deux aspects, les entreprises peuvent bénéficier pleinement des avantages de la production connectée et se positionner comme des leaders de l’industrie 4.0.
Les défis de l’industrie 4.0
L’essor de l’atelier 4.0 s’annonce comme la promesse d’une nouvelle ère industrielle, mêlant connectivité, automatisation et intelligence artificielle. Toutefois, si cette mutation vers un atelier connecté offre de nombreuses opportunités, elle présente aussi des défis majeurs que les entreprises doivent surmonter.
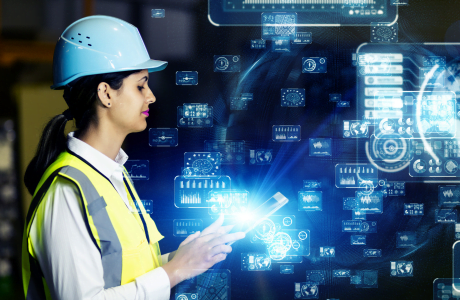
Sécurité et confidentialité des données:
Dans un atelier 4.0, où machines et systèmes sont interconnectés, la circulation massive des données peut être une aubaine pour les cybercriminels. Avec la mise en réseau d’équipements de production, de systèmes de surveillance et de plateformes de gestion, la question de la sécurité des données devient centrale. Assurer la confidentialité des informations, protéger les systèmes contre les intrusions et garantir l’intégrité des données sont des impératifs dans le monde connecté de l’industrie 4.0. Les responsables de l’atelier doivent constamment être à jour avec les dernières mesures de sécurité pour éviter toute vulnérabilité.
Investissements technologiques et formation:
Le passage à un atelier 4.0 nécessite des investissements conséquents en matière de technologie. L’acquisition d’équipements connectés, l’implémentation de systèmes de gestion intelligents et la mise en place d’infrastructures de réseau robustes sont des étapes cruciales. Parallèlement, la formation des employés pour qu’ils s’adaptent aux nouvelles technologies de l’atelier connecté est essentielle. Il ne suffit pas d’avoir les outils les plus avancés; il faut également que l’équipe soit compétente pour les utiliser efficacement.
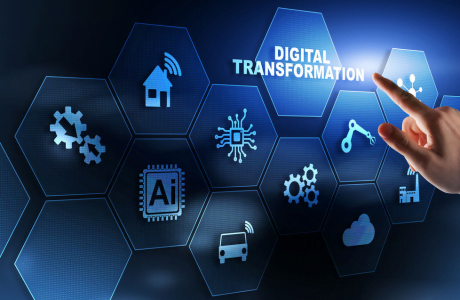
Intégration culturelle et organisationnelle:
Le concept d’atelier 4.0 bouleverse non seulement les modes de production, mais aussi la culture organisationnelle. L’introduction de technologies connectées et de systèmes automatisés peut engendrer des résistances parmi les équipes habituées aux méthodes traditionnelles. Sensibiliser les travailleurs à la valeur ajoutée de l’atelier connecté, intégrer leurs retours dans les processus de transformation, et garantir une transition en douceur sont autant d’enjeux que les dirigeants doivent prendre en compte.
En conclusion, bien que l’atelier 4.0 représente la prochaine étape logique de l’évolution industrielle, son adoption n’est pas sans défis. Les entreprises doivent être préparées, tant sur le plan technologique qu’organisationnel, pour exploiter pleinement les avantages de l’atelier connecté tout en naviguant prudemment à travers les obstacles inhérents à cette transition.
Peut-on connecter nos ateliers sans lourd investissement ?
Pourquoi est-il crucial de considérer l’Atelier Connecté aujourd’hui?
L’ère de l’industrie 4.0 et de l’atelier connecté s’est imposée comme la norme dans le paysage industriel moderne. Les entreprises qui ne suivent pas cette tendance risquent de se retrouver à la traîne. Mais face à la crainte d’investissements onéreux et de changements déstabilisants, comment une PME peut-elle amorcer cette transition sans se ruiner ni prendre de risques inconsidérés ?
Est-ce que les méthodes traditionnelles entravent votre productivité?
Les petites et moyennes entreprises sont souvent submergées par la fragmentation de l’information. Entre les feuilles Excel dispersées, les emails interminables et les interruptions constantes pour des sollicitations directes, la fluidité des opérations est compromise, rendant chaque tâche laborieuse et chronophage.
Comment We Are Team peut-il être votre tremplin vers un atelier moderne?
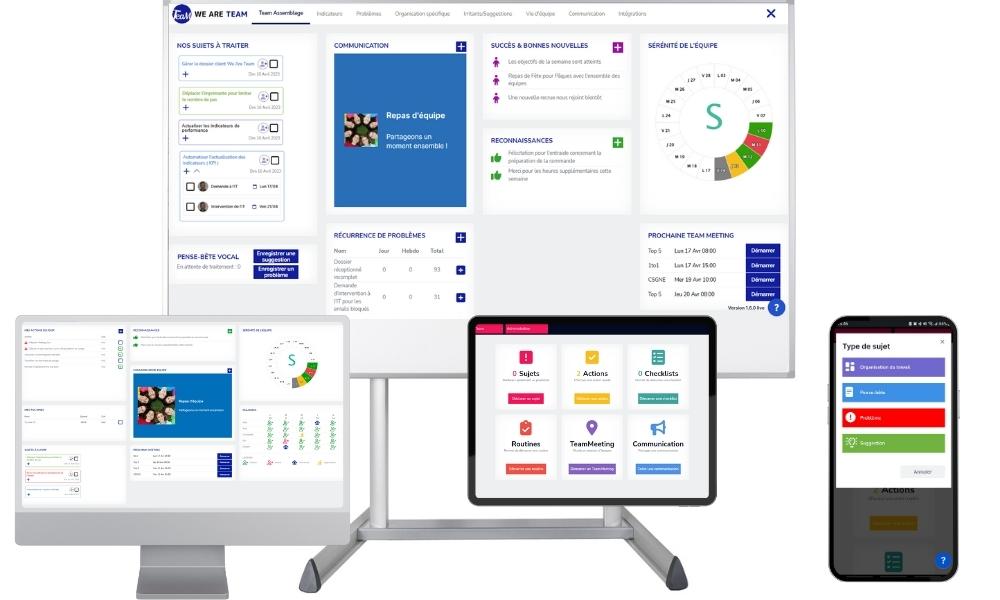
Qu’est-ce que la solution SaaS de We Are Team a de si spécial?
We Are Team transforme radicalement la gestion de vos opérations. Notre plateforme SaaS a été conçue pour capturer, visualiser et animer les informations et actions opérationnelles qui se perdent habituellement dans le chaos quotidien. C’est terminé d’oublier une action, vous serez alertés en cas d’incident et vous pourrez suivre toutes les demandes ou actions de chacune des équipes. Nous rendons la solution accessible à l’ensemble de l’entreprise, des RH aux opérateurs proche des moyens de production.
De plus, la plateforme s’adapte à vos métiers, vos processus et votre terminologie. Vous pouvez personnaliser les fonctionnalités selon les besoin de chacune de vos équipes. Nous nous adaptons à vos fonctionnements, et non l’inverse.
Quels sont les avantages tangibles de notre plateforme?
Imaginons un monde où la remontée d’informations est simplifiée grâce à un mobile où vous pouvez simplement prendre une photo, ajouter un tag ou enregistrer un message vocal. Il n’est pas nécessaire d’écrire ni d’avoir un ordinateur à portée de main. Nous sommes conscients que les déplacements sont au frein au changement, c’est pire encore si vous donnez un clavier à vos collaborateurs.
Aussi, nous rendons simple l’accès à l’information depuis le téléphone et des écrans idéalement tactile pour interagir et améliorer la collaboration. Visualisez vos tableaux de bord qui vous montrent clairement les priorités, les points de blocage et l’avancement des tâches de toute l’équipe. C’est ce que nous offrons, et plus encore.
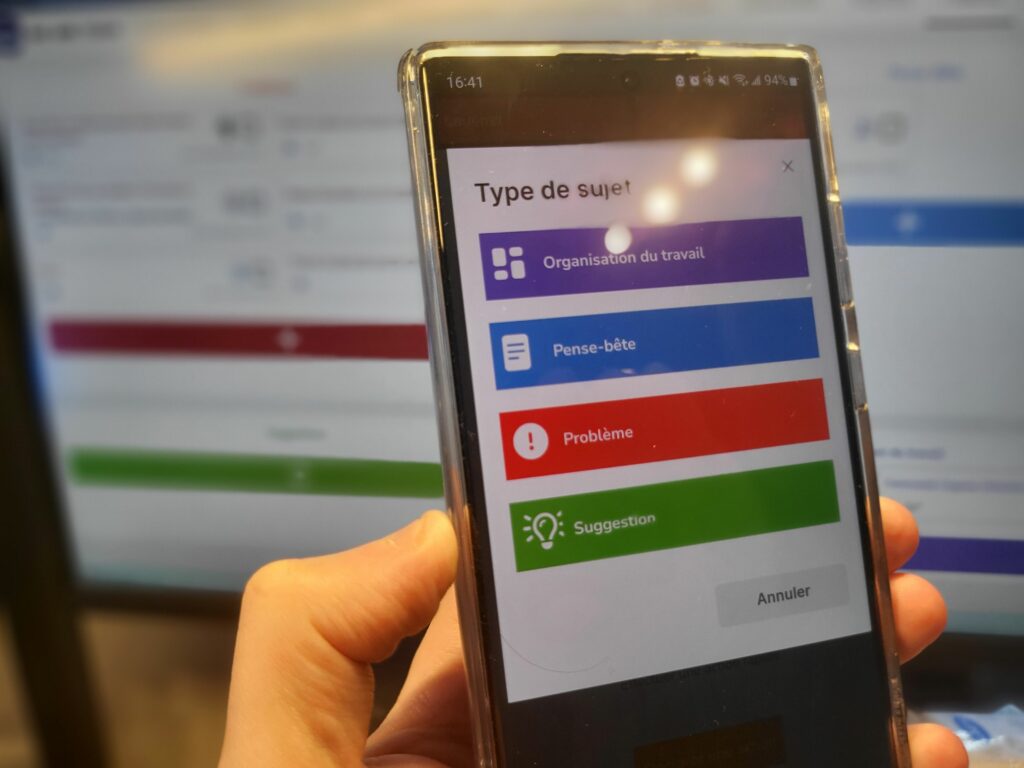
Comment vous assurer que cette transition se passe sans encombre?
Notre équipe, forte d’experts en Management, Lean et Excellence Opérationnelle, est là pour vous guider. Que ce soit à travers des ateliers participatifs, du coaching, de la formation ou un suivi régulier, nous sommes à vos côtés à chaque étape.
Le déploiement se fait par équipe avec une réflexion initiale dans laquelle nous impliquons vos collaborateurs. Nous paramétrons l’application avec vous en utilisant votre terminologie. Notre support est disponible en continu et nous assurons un coaching hebdomadaire au démarrage, pour vous garantir la meilleure appropriation possible.
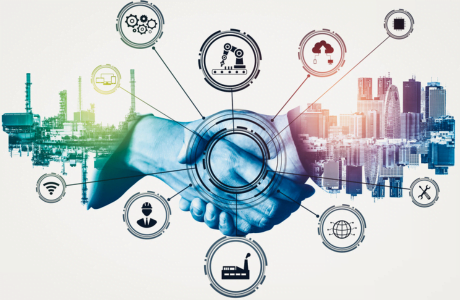
Est-il vraiment rentable d’adopter notre solution?
En plus de notre promesse d’un déploiement sur mesure en seulement 4 heures, chaque collaborateur de votre entreprise économisera plus de 40 heures par an. Et le retour sur investissement ? Vous le verrez en seulement 3 mois, avec un abonnement dès 8 Fr par utilisateur.
Comment est-ce possible ? En supprimant des déplacements et des interactions à travers les appels, sollicitations directes ou demandes internes.
Conclusion sur l’atelier 4.0 :
L’industrie a connu une transformation rapide et profonde depuis l’avènement de l’industrie 4.0. Ce mouvement, né de la fusion entre les technologies numériques avancées et les méthodes de production traditionnelles, a ouvert la voie à une ère nouvelle de fabrication intelligente et connectée. Les avantages sont innombrables : une augmentation de la productivité, une meilleure réactivité aux besoins changeants du marché, une gestion optimisée des ressources, et surtout, une capacité accrue à innover rapidement face à une concurrence mondiale.
La mise en œuvre de l’industrie 4.0 n’était initialement à la portée que des grandes multinationales dotées de ressources considérables. Cependant, avec le temps, le paysage a évolué. De nouveaux acteurs ont émergé, ayant pour mission de démocratiser l’accès à ces technologies révolutionnaires. Ces acteurs ont développé des solutions flexibles, adaptées et abordables, spécialement conçues pour répondre aux besoins et aux contraintes des petites et moyennes entreprises (PME). Ainsi, les PME peuvent désormais bénéficier de l’efficacité opérationnelle de l’industrie 4.0 sans supporter les coûts prohibitifs initialement associés.
Alors que le monde industriel continue d’évoluer, il est essentiel pour les entreprises, quelles que soient leur taille et leur envergure, de rester à la pointe de cette révolution. Pour celles qui cherchent à amorcer cette transition, ou à optimiser leur approche actuelle, il existe des solutions collaboratives, conçues pour canaliser, centraliser et solutionner les défis opérationnels quotidiens. Des plateformes qui simplifient la communication, visualisent les priorités et centralisent les actions, tout en étant supportées par une expertise solide en management et excellence opérationnelle.
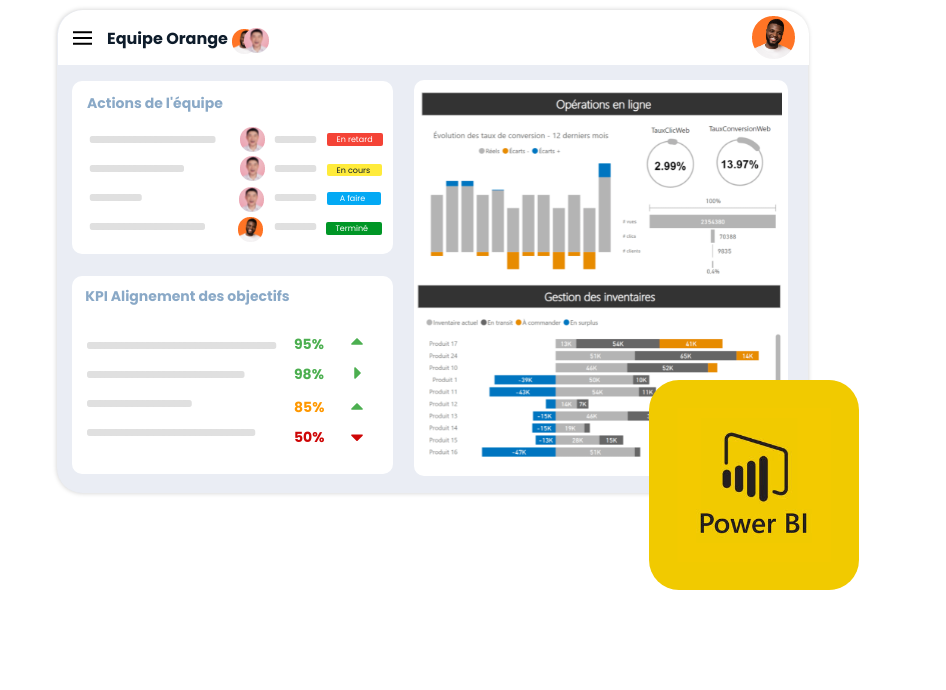
Face à l’avenir de la production connectée et à un monde industriel en perpétuelle mutation, il est temps de poser la question : êtes-vous prêt à transformer votre atelier pour le positionner à l’avant-garde de l’innovation ?